How to Strategically Implement the PDCA Methodology in Your Food Safety Management System.
- Rayki Goh
- Jan 27
- 7 min read
Updated: Jan 30

Hey Geeks,
Managing a robust food safety system requires more than just knowledge—it demands strategic leadership and structure.
The rule of thumb for managing a tight food safety management system is to appoint a manager who is academically qualified in food science, has a background in food safety management or a related scientific discipline, and has completed certification courses in food safety management.
To ensure impartiality and provide a fresh perspective during internal audits, the manager appointed to lead the food safety team should not be involved in daily operations.
The Plan-Do-Check-Act (PDCA) methodology provides a structured framework to help organisations sustain their food safety management system effectively. When applied correctly, it ensures the system functions within a sustainable ecosystem with minimal disruptions. If you are unfamiliar with the PDCA methodology, consider starting with this introductory guide.
To apply PDCA in practice, assign managers to two distinct teams: one focusing on food safety compliance and the other overseeing food operations. This division establishes an effective system of checks and balances.
Here’s a table illustrating the divisions and their respective responsibilities:
Phase | Role | Criteria | Responsibilities |
---|---|---|---|
Plan | Food Safety Manager | Academic background in food science or equivalent with professional food safety certification training | Hazard assessment, proposing controls, training staff. |
Do | Operations Team | Involved in daily operations with training in food safety management and experience in carrying our control measures | Implementing controls approved by the food safety team, periodic team briefing. |
Check | Food Safety Team | Academic background in food science or equivalent with professional food safety certification training | Auditing and verifying compliance, re-training on non-conformance. |
Act | Operations Team | Involved in daily operations with training in food safety management in proposing corrective and preventive actions | Proposing and executing CAPA, with food safety team approval. |
An infographic illustrating the Plan-Do-Check-Act framework and how the respective roles and responsibilities play a part in the management system ecosystem.
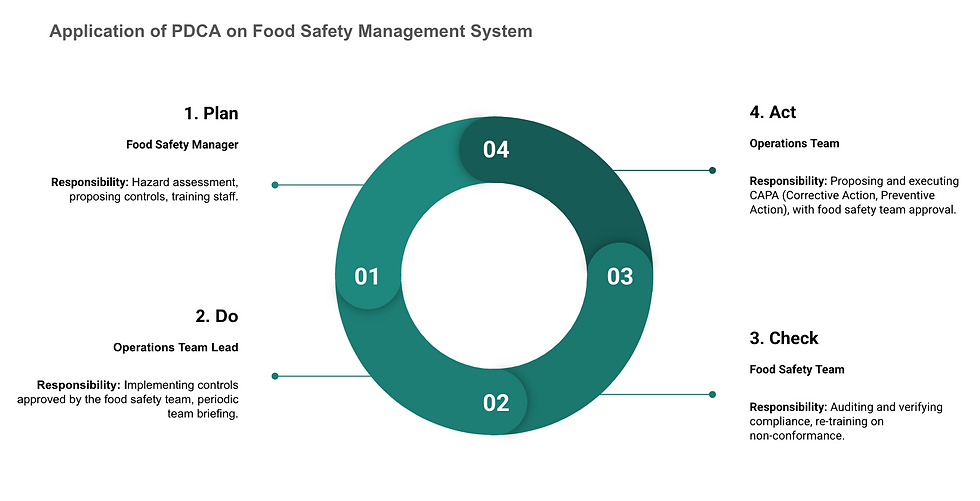
The 3 Main Reasons Why the Food Safety Manager Shouldn’t Propose CAPA (Corrective Action, Preventive Action)
While the FSQ manager possesses technical expertise, they may lack the operational context needed to propose practical and effective solutions for specific workflow issues.
The involvement of operations managers highlights their competency in food safety, which is crucial for ensuring the entire team adheres to food safety standards.
A collaborative approach—where operations propose CAPA and food safety provides approval—enhances teamwork and ensures that solutions are both compliant and operationally viable.
I’ve found this approach to be the most strategic based on my years of observing food safety management systems across 200+ companies I’ve either consulted for or audited.
In my experience, some companies struggle with implementation that’s lopsided—either operational managers are barely involved in the food safety management system, or the operations team takes full control over how it’s implemented.
This kind of imbalance often leads to a system that simply doesn’t last.
The Strategic Framework Helps You:
Optimises team strengths: Roles are aligned with expertise and responsibilities.
Empowers managers: Encourages accountability and proactive problem-solving.
Enhances collaboration: Fosters a unified approach to food safety.
Drives continuous improvement: Ensures the organisation learns and evolves.
Sustains compliance: Maintains alignment with ISO standards and regulatory expectations.
By adopting this approach, the organisation ensures that food safety is not just a compliance exercise but an integral and sustainable part of its operations. This strategic rationale also helps future-proof the organisation by embedding food safety into the culture and daily practices of the operations team.
A more effective strategy is to separate compliance and operations into two dedicated teams, each with distinct KPIs. Staggering the responsibilities of these teams allows for better alignment and collaboration. This approach thoughtfully applies the PDCA (Plan-Do-Check-Act) methodology by balancing expertise, operational efficiency, and teamwork.
Once you understand the key elements of an effective PDCA framework & strategic food safety planning, the next step is to implement it in a way that ensures both compliance and operational goals are met seamlessly.
In the ‘Plan’ Phase: Food Safety Manager
In the Plan phase, the FSQ manager takes charge of assessing potential hazards, whether microbiological, physical, or chemical, using their scientific expertise and systematic approaches like HACCP or in higher standards like the ISO 22000 or the FSSC 22000.
The FSQ Manager (also known as the Food Safety Team Leader) sets control measures as part of the hazard analysis that align with legal and standard requirements, ensuring compliance and effectiveness.
Once these measures are established, the FSQ manager clearly communicates the expectations to the operations team, outlining what needs to be implemented, how it should be monitored, and why it is critical to food safety.
The FSQ manager will entrust the role of implementing and monitoring these measures to the operations team, trusting them to integrate the controls into daily practices and ensure consistent adherence within the workflows.
This collaborative approach ensures that the controls are practical, effectively implemented, and properly maintained across operations.
In the ‘Do’ Phase: Operations Team
In the Do phase, the operations team is either led by the production manager or an operations manager, who takes charge of implementing the food safety controls decided during the planning stage.
Being directly involved in daily operations, they are in the best position to oversee how these measures are integrated into workflows.
Their hands-on role ensures that staff receive proper training and that the controls are consistently maintained. With their in-depth knowledge of production schedules, workflows, and equipment, they can seamlessly incorporate these measures into operational processes.
It is logical for the operations manager to handle this phase, as they are closely connected to the day-to-day activities and are ideally placed to influence the implementation of food safety practices.
In the ‘Check’ Phase: Food Safety Team
In the Check phase, the food safety team takes on the crucial task of verifying whether the food safety controls implemented during the Do phase are actually working as intended.
This involves conducting audits, inspections, and ongoing monitoring to ensure everything is on track. Their job is to evaluate if the controls were applied correctly and whether they are consistently being maintained in practice. Along the way, they also look out for any deviations or areas that need improvement.
What makes this phase particularly important is the objectivity the FSQ manager brings to the table. Since they are not directly involved in the day-to-day operational implementation, they can provide an unbiased perspective.
Their role goes beyond simply pointing out what’s wrong; it’s about assessing compliance, identifying non-conformities, and documenting findings so these can be addressed through corrective action planning and further discussions.
This phase is all about ensuring the system remains robust and continuously improves.
In the ‘Act’ Phase: Operations Team
In the Act phase, the responsibility for proposing and implementing corrective and preventive actions (CAPA) rests with the operations team.
The initiative is usually led by either thre production manager or the operations manager. This makes sense because they have an in-depth understanding of the workflows and are best positioned to identify root causes of issues, whether it's equipment malfunctions, inefficiencies in processes, or other operational challenges.
Their familiarity with the day-to-day realities allows them to propose solutions that are practical and achievable, rather than theoretical fixes that might not work in practice.
By taking ownership of CAPA, operations managers become active contributors to the organisation's food safety goals, fostering a culture of accountability. This approach ensures they’re not just following instructions but are genuinely invested in preventing future non-conformities.
Once the operations team proposes their solutions, the FSQ manager steps in to review and approve them, ensuring they meet food safety standards and align with regulatory requirements.
This collaborative process avoids overloading the FSQ manager while empowering the operations team to play a central role in maintaining food safety, creating a balanced and effective system.
WHAT DOES THIS MEAN?
Ultimately, the PDCA strategy is most effective when the compliance and operations teams work in harmony, though some level of segregation is necessary to ensure checks and balances.
Top management must show their support for the framework and stay actively involved in every phase of the process.
Curious about why food safety is vital for your business? Read the next article here.
Or perhaps a related read: Discover the Secret Behind the World-Renowned Management Model: Learn the PDCA in Just 1 Minute.
Until next time~

About the Writer:
Comentarios